I’m Picking Up Bad Vibrations: Designing Tools for Safer Jet Engines
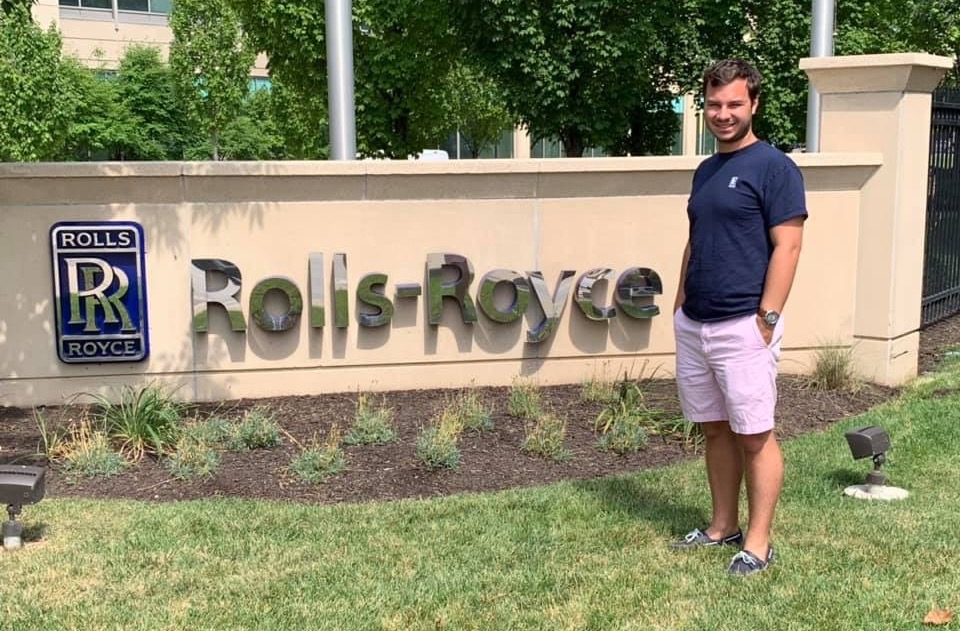
Guest post: Richard Hollenbach III is a Ph.D. candidate at Duke University and a 2020 and 2021 NC Space Grant Graduate Research Fellow.
On the average day, over 1.7 million Americans hop on an airplane to conduct business, visit family or go on vacation. But when you sit in your seat, do you ever look out the window and wonder how the engines work? More importantly, how are they improved upon? The Aeroelasticity Laboratory at Duke University is one of the places where cutting-edge research meets pressing aerospace industry needs, to ensure aircraft design is constantly improving.
Background
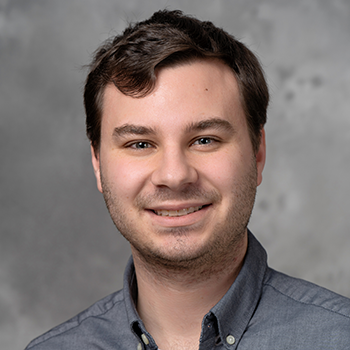
I was not always in the aerospace engineering field; in fact, two of my first research projects involved biomechanics and nuclear reactor channels. However, I spent my junior summer as a National Science Foundation REU (Research Experiences for Undergraduates) student at Texas A&M University in the Aerothermochemistry and Hypersonics Laboratory. I was hooked: not only did I get to assist the graduate students in running hypersonic wind tunnels, but I also created a laser spectrometer to use in plasma analysis. We also simulated the reentry of space shuttles on a computer simulation and then compared it in the tunnel!
I decided to find a graduate program that would allow me to conduct experiments in wind tunnels and teach me cutting-edge computational fluid dynamics techniques. In addition, I wanted to solve issues in aerospace coming directly from industries, so I chose to attend Duke University. Duke is fortunate to have a plethora of top-notch faculty members, who have received honors from the American Society of Mechanical Engineers (ASME), American Institute for Aeronautics and Astronautics (AIAA) and more.
One of these prestigious faculty members, Robert Kielb, the Professor of Practice in the Department of Mechanical Engineering & Materials Science, also serves as the director for the ‘GUIde’ Consortium of Turbomachinery Aeroelasticity. Formed in the early 1990s, this group brings together Governmental entities (NASA), Universities (Duke, Purdue, University of Michigan, Leibniz University of Hannover and more) and Industries (Rolls-Royce, Pratt & Whitney, Honeywell, General Electric and more) to solve some of the most challenging problems in aerospace engineering.
One of these problems was observed by Dr. Kielb when he worked for NASA and General Electric. A particular set of vibrations were measured at different operating conditions than other well-researched issues; they were labeled as Non-Synchronous Vibrations, or NSV. Ever since the turn of the millennium, Dr. Kielb has studied this phenomenon, along with faculty and graduate students at Duke in the Aeroelasticity Laboratory.
Present
Why care about NSV? Well, there are currently no tools out there to predict it. When an engine is built and tested, it either works correctly or fails. This wastes lots of money, time and energy all for a failed engines. The key questions are, what causes NSV and what can we do to prevent it? These are the basic research questions I have been tasked with solving during my Ph.D. journey at Duke. Over the past two decades, a few major insights have been unlocked about this aerospace issue. Some people are familiar with the vortex shedding phenomenon of flow over a cylinder, like a smoke stack (see the first graphic below); many might also recognize that when objects are excited at their natural frequencies, they vibrate at high levels like a tuning fork (see the second graphic below). NSV can be caused by these two occurring together, mainly when the shedding frequency matches the natural frequency.
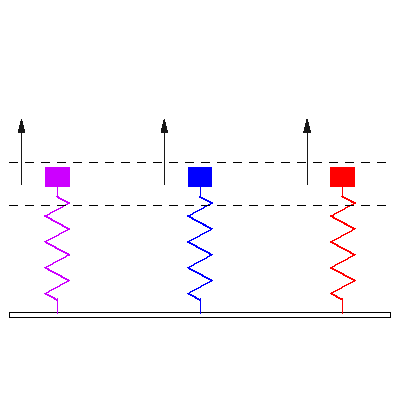
However, what makes NSV significantly more dangerous is that there is an entire engine operating region where NSV can occur. In this region, the shedding frequency “locks-in” to the natural frequency, leading to large vibrations. Far away from this phenomenon is the “unlocked” state where the vibrations are no longer dangerous; you can see these two conditions below.
What makes this research project especially engaging is that I am utilizing a three-fold approach to solve it: experimental, computational and numerical. The first one allows me to experiment in our own low-speed wind tunnel. I am measuring the pressure on an airfoil’s surface to experience NSV conditions. In addition, I am mentoring undergraduate and master’s students in our lab group in the development of other turbomachinery experiments. Finally, I am supporting the design and testing of a turbine experiment being built in Germany. Hopefully, before I graduate, I will get to visit the turbine rig to assist with the data collection.
While conducting experiments provides hands-on research that I enjoy, I also like utilizing novel computational tools such as supercomputer fluid simulations. To validate our experiments, we run computational fluid dynamics simulations on the same geometry to compare data. To speed up the solving time, we utilize supercomputing clusters around the country.
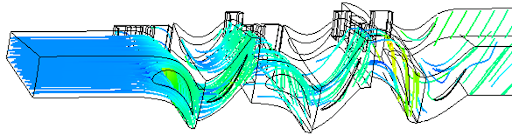
The last piece of the puzzle is to devise numerical tools for engine manufacturers to use to ensure there is no potential for NSV in their final designs. As a result, I am creating simplified models in MATLAB to point manufacturers to safe and NSV-free designs for their compressors and turbines.
Future
In the short term, I will be aiming to finish up this project in 2022, identifying potential next steps for future students to complete in this quest to solve the problem of non-synchronous vibrations. My results will also become available to the engine manufacturers in the Guide Consortium, in order to build NSV-free engines.
As for me, I am looking into becoming a consultant in the aerospace and defense sectors. I want to be able to apply my research skills to solve some of the most challenging problems faced by our society today.
- Categories: